How HVO Fuel is Made and How It Reduces CO₂ Output
Hydrotreated Vegetable Oil (HVO) is a low-carbon diesel alternative that greatly reduces CO₂ gas emissions when compared to diesel. Diesel fuel, relies on crude oil extraction and refining. Where as HVO fuel is produced from renewable feedstocks, such as waste vegetable oils and animal fats. Other feedstocks for HVO fuel include commercially grown sources like biomass crops.
HVO fuel reduces CO₂ emissions across the entirety of its lifecycle, from sourcing and procuring feedstocks to combustion in vehicles, by eliminating the need for crude oil. Many studies agree that HVO can achieve up to a 90% reduction in greenhouse gas emissions when compared to traditional diesel, making it an essential solution in the transition to net-zero emissions for the transport and logistics sector.
These emission reductions don’t just look good on paper — they’re recognised under the Renewable Transport Fuel Obligation (RTFO), the UK’s official scheme for incentivising low-carbon fuels. RTFO compliance allows suppliers to issue tradeable credits (RTFCs), helping to reduce costs while meeting environmental targets.
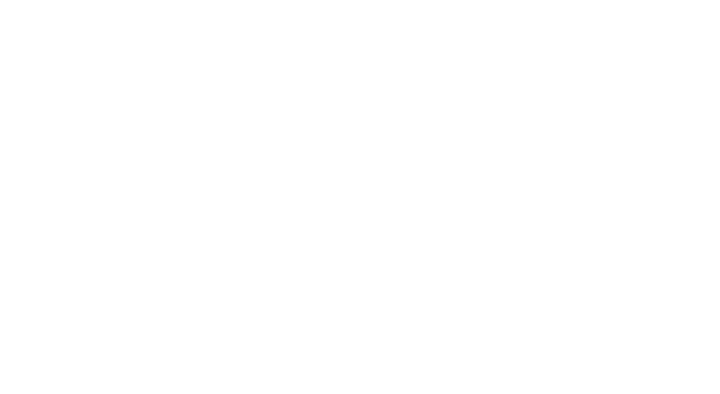
How HVO is Made: Step-by-Step Breakdown
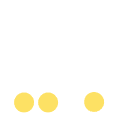
1. Feedstock Collection & Preparation
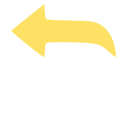
2. Hydrotreatment Process: Converting Oils into Fuel
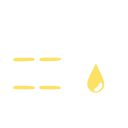
3. Isomerisation and Hydrocracking: Optimising Fuel Properties
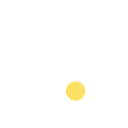
4. Final Refining and Certification
HVO production centres around hydrotreatment, a chemical process that removes oxygen from feedstocks using hydrogen.
1. Feedstock Collection and Preparation
HVO is made from waste-based and renewable feedstocks, including:
-
- Used cooking oils
- Animal fats
- Technical corn oil
- Tall oil pitch (a by-product of wood processing)
- Residues from vegetable oil processing
These feedstock are gathered and undergo a pre-treatment process, which includes filtering and removing contaminants. These feedstocks must meet strict criteria for sustainability and traceability. The ISCC certification ensures every stage — from sourcing to refining — meets internationally recognised environmental and social standards.
2. Hydrotreatment Process
Converting Oils into Fuel
The purified feedstocks undergo hydrogenation, where hydrogen is used to eliminate oxygen, sulfur, and nitrogen.
Conditions:
- Temperature: 280-450°C
- Pressure: 1-5 MPa
- Catalyst Used: Nickel-Molybdenum (NiMo)
This stage includes three key reactions:
- Hydrodeoxygenation – Removes oxygen molecules to form hydrocarbons.
- Decarbonylation & Decarboxylation – Removes carbon-based compounds, further refining the fuel.
3. Isomerisation and Hydrocracking
Optimising Fuel Properties
Molecules are restructured to enhance fuel properties, improving cold-weather performance and combustion efficiency.
HVO’s high cetane number (70-90 vs. 51 for conventional diesel) ensures complete combustion, reducing CO₂ emissions per kilometer driven.
4. Final Refining and Certification
The refined fuel undergoes rigorous quality testing to ensure compliance with sustainability certifications:
- RTFO (Renewable Transport Fuel Obligation – UK government framework)
- ISCC (International Sustainability & Carbon Certification)
- Zemo Partnership Renewable Fuels Assurance Scheme
Once certified, HVO is distributed for use in public and private fleets.
Lifecycle CO₂ Emissions of HVO Fuel vs Conventional Diesel
All values are approximate and based on literature sources including the Neste Renewable Diesel Handbook)
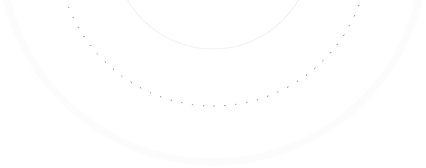
Key Takeaways
Feedstock Matters:
HVO made from waste oils & residues has the lowest emissions (~150 kg CO₂/tonne) because it repurposes existing materials.
Crop-based HVO (palm, soybean, rapeseed oils) has higher emissions (~500+ kg CO₂/tonne), due to land use and farming emissions.
Refining Process is Lower-Carbon:
Fossil diesel refining emits 700–2,800 kg CO₂/tonne due to crude oil processing.
HVO refining emits 200–600 kg CO₂/tonne, mainly from hydrotreating which requires hydrogen (derived from natural gas or electrolysis).
End-Use is Nearly Carbon-Neutral:
HVO’s tailpipe CO₂ emissions are close to zero because the carbon released was originally absorbed by the biomass feedstock, unlike fossil diesel.
Overall Reduction:
HVO fuel cuts 75–90% of total CO₂ emissions compared to diesel, depending on feedstock choice and refining method.
Carbon Sequestration and the Closed-Loop Advantage
One of HVO’s unique advantages is that it supports a near-closed carbon cycle:
- The plants used to produce HVO feedstocks absorb CO₂ during their growth cycle.
- When HVO is burned, it releases the same CO₂ absorbed during feedstock cultivation.
- This cycle drastically lowers net CO₂ emissions, compared to fossil fuels, which release stored carbon from millions of years ago.
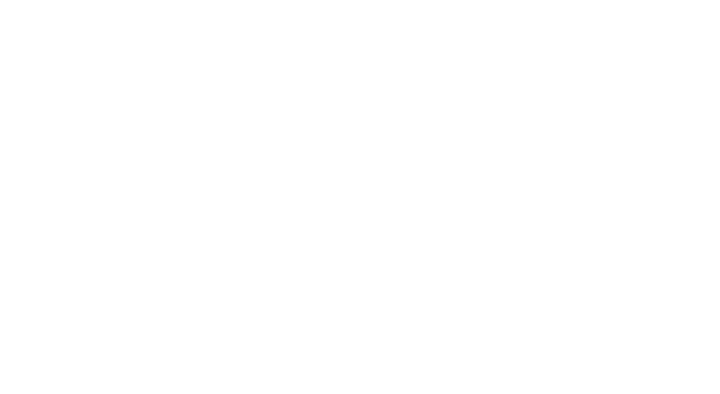
Additional Benefits: Efficiency & Performance
Higher Energy Content
Some studies indicate lower fuel consumption per mile
Superior Combustion
More complete burning, reducing unburned hydrocarbons and particulate matter
Better Cold Weather Performance
Unlike fossil diesel, HVO does not gel in cold temperatures, ensuring smooth operation year-round.
Considerations and Limitations
While HVO presents a major step toward decarbonisation, its impact depends on:
Feedstock sourcing
Waste-based HVO has 5 g CO₂e/MJ, whereas palm-based HVO can be as high as 102 g CO₂e/MJ.
Scalability
HVO production is growing but still represents a fraction of total fuel demand.
Long-term role
HVO is best viewed as a transitional fuel alongside electrification and hydrogen solutions.
“HVO fuel represents a practical, scalable, and near-zero carbon solution for fleet operators, businesses, and government agencies seeking to reduce emissions without requiring new vehicle investments. By eliminating the need for crude oil extraction and improving combustion efficiency, HVO delivers up to 90% lower CO₂ emissions compared to fossil diesel.
For public sector fleets looking to ensure these emissions savings are credible, the Zemo Renewable Fuels Assurance Scheme (RFAS) provides independent verification that HVO suppliers meet strict sustainability and greenhouse gas reduction standards.”